Sunday, 14 November 2010
Sunday, 2 May 2010
Mission
Presentation











If anyone would like to have a look at how to assemble the crane please contact James Baddeley for a demonstartion of the model.
Pulley System
Saturday, 24 April 2010
Conclusion
- Our designs are simple and cost effective meaning more value for you the consumer
- We are a company concerned with looking after people and the environment by cutting down on our carbon footprint
- With rapid production abilities you will soon be ready for anything
We thank you for your time whilst looking at our tender proposal and hope to hear from you in the near future.
Thursday, 22 April 2010
Materials selection
Construction Manual
- Legs x4 (numbered 1 - 4)
- Leg joints x2
- Beam x2 (numbered 5&6)
- beam joint x1
- Standard Bolts (with nuts) x8
Wednesday, 21 April 2010
Design of components
- Weight - Each component would need to be light enough for a person to carry.
- Ease of use - The whole assembly would need to be assembled and dissassembled without specialist knowledge. The assembly uses a simple idea with very few components.
- Adaptability - The crane would need to adapt to the environment it is in. If the ground is uneven, a series of holes in the beams allow for making the legs longer/shorter.
- Robustness - Each component was designed with the forces that will be acting on it in mind. The materials we have used are robust enough to hold the load.
- Cost - The cost of each component was taken into account as there is very little point in having a disaster relief crane that costs a fortune to produce. Wood is very heavy but is very cheap too, this is why we picked this material over metals.
- Size - Each component was designed to fit in or on a Land Rover. The metal components would easily fit in the back of the vehicle and the beams would be able to go on the roof rack without obstructing the drivers view or causing any hazards
- Repair - We used wood for the beams because they are easily replaced with a material that may be in the disaster area without the need for specialist tools. The beams would be under the most stress so therefore we made these replacable. If a joint was to break then a replacement would be needed and for this reason we have chosen to use steel to decrease the chance of damage.
CAD Design and Rendered Image
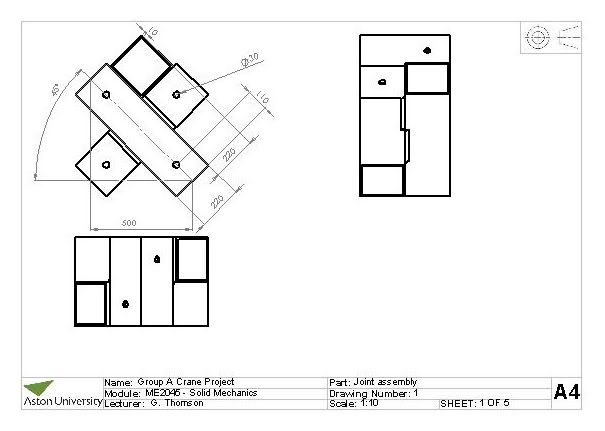



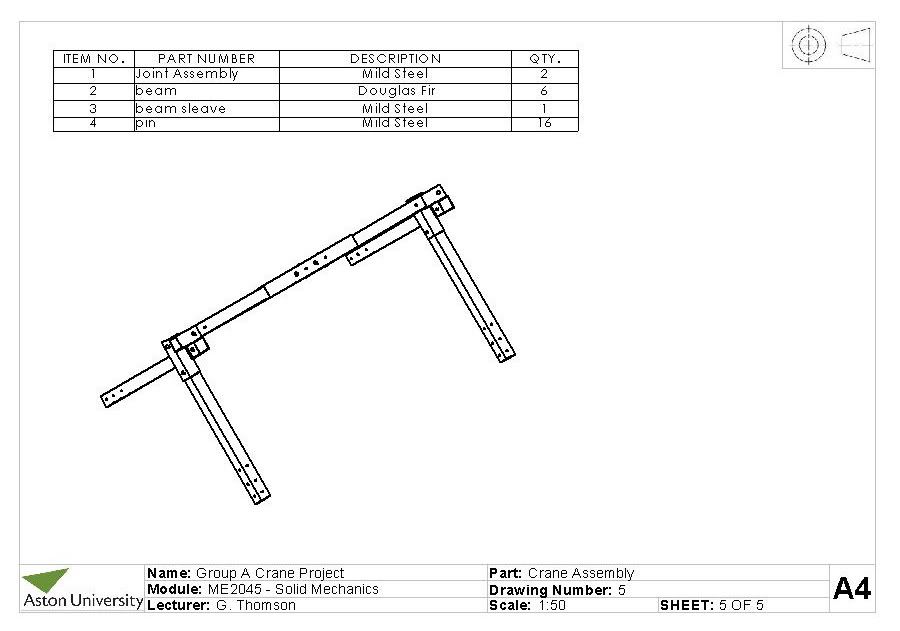
This is a rendered image of what the crane will look like:

Financial Report

The Cost to buy a Crane will be £1200.00
For Just the Joints the cost will be £600
To Rent the crane will cost £100 per week
Prices are excluding VAT because it is for humanitarian use.
Components from:
- http://www.cornwallwood.co.uk/products/16__bulk_sawn_timbers_treated_/index.html
- http://www.metals4u.co.uk/detail.asp?cat_id=50&prd_id=2110
- http://www.tooled-up.com/Product.asp?PID=153418
- http://www.metals4u.co.uk/detail.asp?cat_id=1376&prd_id=6618
- http://www.metals4u.co.uk/detail.asp?cat_id=1376&prd_id=4739
- http://www.screwfix.com/prods/68784/Hand-Tools/Load-Handling/Duplex-Sling-3-Tonne-4m
Patents will be taken out to protect the pulley system which will be our trade secret stopping people from copying our design.
Tender Proposal Intro
Our crane will allow the user to pick up and move rubble over a distance meaning that people trapped underneath can be rescued. It will also be easy to disassemble into small pieces which will allow it to be put into the back of a Land Rover for ease of transport into the crisis area.
The crane shall be made of a mixture of wood and metal. We have chosen to make the majority out of wood because of the overall reduced weight and cost of the material. By having a lighter material the crane will be easy to carry short distances without having to disassemble it first; being able to move faster means more people can be saved.
Due to the likely-hood that there will be a lack of power in the area the crane will use hand-powered pulleys and cranks in order to move the rubble. This again helps cut down on the complexity and ultimately the cost of the finished product and means that there is less to go wrong which in such a critical environment is a key factor.
The simple design of the crane means it can be produced both rapidly and at a low cost providing the best possible value for you. Furthermore it is quick to assemble and easy to use ensuring many people can be trained in its use as quickly and as easily as possible.
As an added bonus and to make up for the trees that are cut down we will plant 10 trees for every crane you buy which in turn will reflect well on you.
ECS, rebuilding your world.
2 TONNE CHAIN BLOCK

We have chosen the 2 Tonne Chain Block, because it is small lightweight and portable. We have chosen 2 tonne for the same reasons why we chose 3 tonne on the strap as its better to be on the safe side. The chain block also includes mechanical load breaks, hardened alloy steel chains.
Available from Metals4U at the price of £47.91 per unit
Webpage: http://www.metals4u.co.uk/detail.asp?cat_id=1376&prd_id=6618
Double Thickness Duplex Sling 3 Tonne 4m

We have decided to use the double thickness sling 3 tonne 4m, This was chosen this because the design specification said the crane should be able to lift 1 tonne but just to be in the safe side, it was decided that we would rather be over than under.
The sling also has reinforced Becket eyes at each end which will give greater strength where the pulley is attached.
Available from ScrewFix at the price of £23.45 per unit
Webpage: http://www.screwfix.com/prods/68784/Hand-Tools/Load-Handling/Duplex-Sling-3-Tonne-4m#
Final Concept Idea
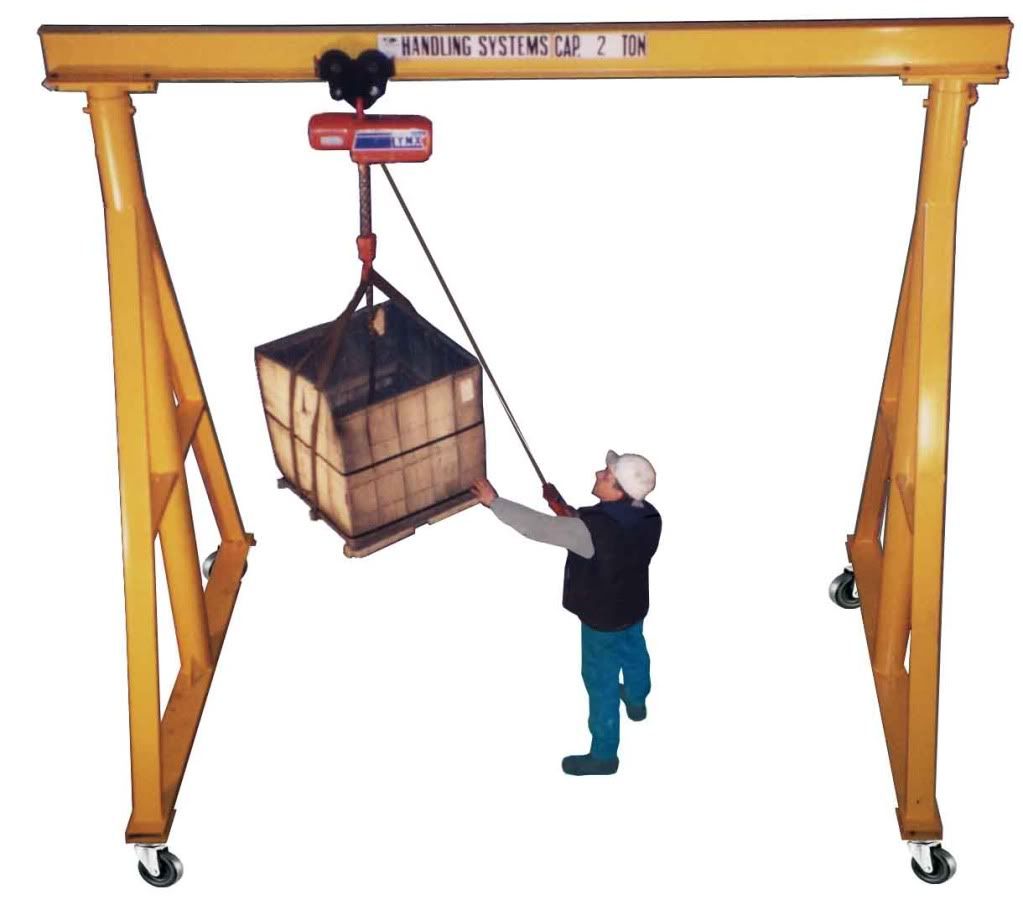
For our final idea we have settled on a type of gantry crane. The problem with a tower crane is that the stresses involved would be very large which would lead to increasing costs and difficulties as we did more to ensure that the design would work.
A gantry crane on the other hand cane be made of far more lightweight material which decreases the cost and the stresses can be easily calculated and compensated for.
Idea Evaluation
Further Ideas
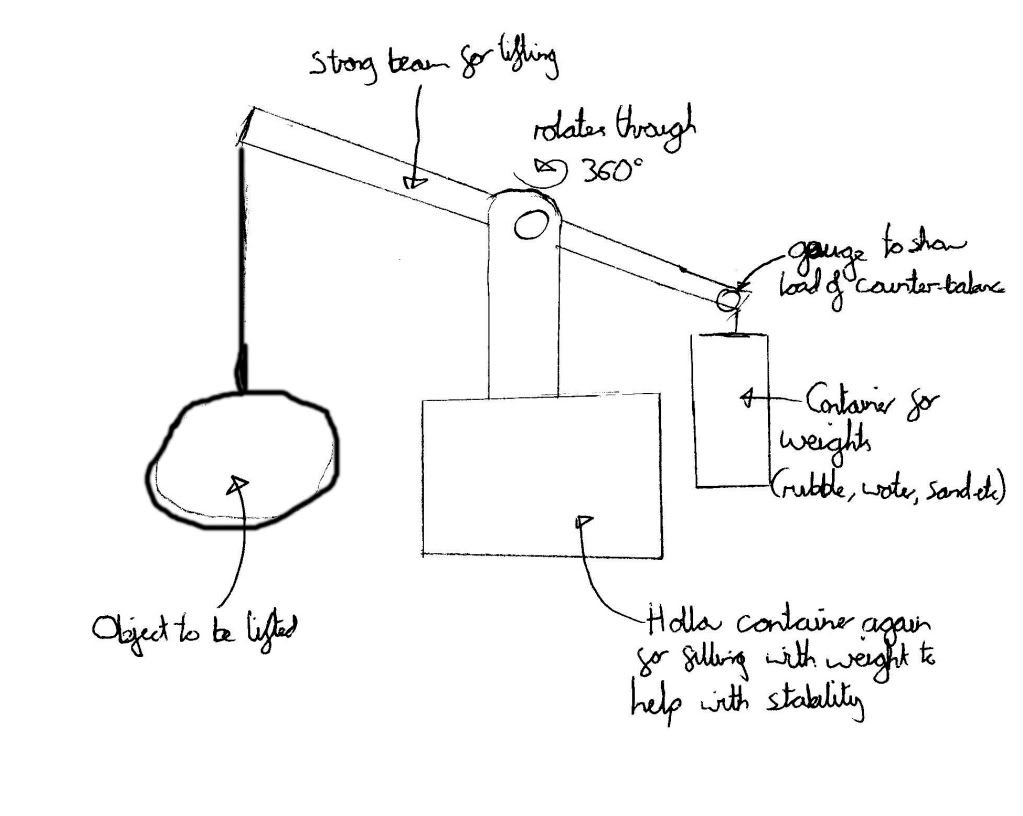
Expanding on ideas already put forward I drew up a sketch detailing both how the crane would work and how the crane would be disassembled in order to fit it into the back of a Land Rover.
This Crane is purely mechanical to prevent any problems should there be a lack of power, which in an earthquake devastated area is rather likely.

Monday, 22 March 2010
initial idea
Crane initial idea:
The design of this crane has been inspired by portable cranes and other application which features a base that fills with water or sand for stability.
The base is meant to be containers that could be filled with water or sand depending on availability.
The tier on each side are also meant to be containers where they can be filled depending on how much wait needed to lift the object.
Workshop Cranes

Workshop Cranes There are several workshop cranes types where each type has a little differences in its characteristics, however they all share the same general principals.
Workshop cranes general advantages:
1. It’s a portable crane
2. Reliable for several industrial applications
3. Small area for storage
4. Easy to move around
5. It operate manually
6. Made of heavy-duty materials
7. One person to operate
Gantry Cranes

Gantry Cranes
Gantry crane is used in most demanding environments where very heavy equipment and machines have to be lifted.
Loader Cranes

Loader Cranes
The Loader Crane is a fixed crane in the back of a truck. Since the carne is fixed, I would eliminate this type of crane considering that we need a portable carne that can be fit into a 4*4 vehicle. However, we could take some ideas of the crane structure itself and use it in our crane design.
Sunday, 21 March 2010
Research Part 1
Friday, 19 March 2010
19/3/10 Minutes
Mohammed Altubayieb
Thomas Anderson
James Baddeley
Richard Bay
Tasks Achieved
- Initial Brainstorming complete. Research on different types of crane, counterbalancing methods and movement methods.
- Individual ideas discussed.
- Evaluated different designs.
Tasks to be completed by 22/3/10
- Individual ideas and diagrams to be uploaded on blog by team members.
- Research page to be uploaded.
- Fully design chosen idea
Next meeting at 5PM 22/3/10
Wednesday, 17 March 2010
Tower Crane ( Base Design )
This is an initial idea for the tower crane base. It consists of several containers that could be filled with any liquid depending on availability. Each container has a volume of 5 gallons, which will give us almost 22.5 kilograms (the weight of each container can various depending on the liquid used).
Sunday, 14 March 2010
Tuesday, 9 March 2010
First Meeting 8.3.10
Project Manager: Peter Armstrong armstpwa@aston.ac.uk
Finance Officer: James Baddeley baddeljc@aston.ac.uk
Chief Designer: Thomas Anderson andersot@aston.ac.uk
Materials Specialist: Richard Bay bayrh@aston.ac.uk
Stress Analyst: Mohammed Altubayieb altubaym.ac.uk